目次へ
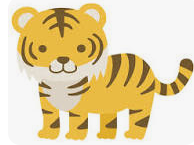
虎は死して皮を残し
プロジェクトてなもんや
ちょっと自慢話を
日本一の工場へ
D産業に関わっておよそ3年後、ある部長さんから福岡県のO市にあるD産業の関連家具工場N社に
コンサルとして出向いて欲しいと要請があった。
あまり気乗りがしなかったが、一度訪ねることにした。
同社の社長に熱心さに打たれ、「この工場を日本一にしてみせます」と見栄を切ってしまった。
以来約30年間この会社と共に歩むことになる。
当時その工場はすべて工場長の指示で製品が作られており、政策図面は1枚も無い。
資材の構成もすべて工場長の頭の中にあって、
資料などどこにもない。
同社の製品は「ノックダウン」と呼ばれる現地組み立てタイプであったため、
1つの製品は6から20ほどの部材で構成されていた。
最初の私の課題はすべての製品の組立図、部品図、加工図、部材リスト、原価計算書などを一から作ることだった。
次は各工程への作業指示書を作らねばならない。
当時はまだ大量生産時代で、生産計画書に応じてひと月の作業指示書を作る。
必要な資材の購入指示書を作り、仕入れ先に発注する。
その一方、現場で働く方への教育も欠かせない。 図面の見方、作業手順の見直しなどを根気よく話し合いながら進めていく。
こうしている間にも世の中の進歩は速度を上げ、大量生産時代は終わり、少量多品種生産へと変わっていった。
そうした矢先、社長から室内ドア専用工場の計画が提案された。 これを私にすべて任せると言われた。
建物は既存のものであるが、十分な広さがある。
ここに日本ではまだ誰も作ったことのない、自動機械を並べた室内ドア生産ラインを作る。
まさに「プロジェクトX」。
毎日木工機械メーカーの技術者や営業担当との打ち合わせ、工場レイアウト図面の書き直しが続く。
機械メーカーもこれまで他車機械とのネットワーク連携やバーコードとデータベースを使った自動運転など経験していないので、
考え方を伝えるだけでも大変だった。
機械を発注し出来上がった加工機械やコンベアの納入が始まると、ほとんど工場に泊まりきり状態になる。
次から次へと難問が発生し、一つの問題を解決するのに何日も何日もかかる。
残念なことにこのプロジェクトに関わった機械メーカーのお二人が、過労がたたったのか亡くなった。
ほぼ1年をかけて工場は完成し、稼働を始めるが、今度は様々なトラブルに見舞われ工場がたびたび止まる。
5年後には受注から生産指示、個別自動加工梱包出荷、売上・請求までの一貫システムが完成した。
同社はそのころ立ち上げた国際営業部でこの工場の製品を中国市場に投入した。
国際合弁プロジェクト
努力は報われず
事の始まりは1999年から。 日本の最大商社M商事が中国への友好記念として一万個の実がなる
トマトとその展示館が北京政府に贈られた。
贈呈式に出席した当時の中国政府建設大臣がその展示館に使われている木製ドアに目をとめた。
「どこの製品か? 」と尋ね、それが日本のN社の製品であることを知る。 早速「これと同じ品質のものを作れる工場を作れ 」と命令を出す。
当然のようにM商事もこのプロジェクトに参加することになり、N社とM商事それに中国側から北京で最大の建材メーカーであったB建材社が合弁プロジェクトメンバーとなる。
N社の代表として私が任命され、M商事北京支局部長とB社の担当重役が日本工場の視察に訪れ、同様の自動化工場を北京市内に建設し、N社は技術指導を行うこととなる。
これから毎月北京でプロジェクトの推進会議を開き、一方工場の設計、機械彫琢方法の検討を進めていく。
プロジェクトの会議はまず事業の市場性、採算性の検討、技術の継承方法などについて、基本的な契約文書の策定から始まる。
どの項目についても双方の思惑があってなかなかまとまらない。
中国側の交渉術は巧みで、午前中の会議の後、昼食会がB社工場内の接待用レストランで豪華に始まる。
度数の高い白酒(バイチュウ)などでほろ酔い加減になって午後の会議となる。
夜は夜で接待の応酬。 お互いが有利に話を進めようと頑張るのである。
このように会議を持つ一方、中国国内での資材調達可能性を探るため、中国側が提案する各地の調達先を視察に回る。
また、中国でこれまで作られてきた木製ドアの制作過程について、既存の工場を見学する。
日本の技術の先進的な面は、軽くて丈夫、さまざまな意匠のものが作れ、施工が容易なことなどで、
今後の中国でのマンション建設需要を見込める。
紆余曲折はあったが、工場図面は完成した。 金具類は当面日本から供給することとして契約締結の寸前、とんでもない問題が発覚する。
この工場で出た利益の日本側取り分がほとんど中国から国外に持ち出せないという。
M商事はこれでは無理だということになり、M商事が手を引くと政治的な問題になりかねないと
N社にプロジェクト幕引きの役目を押し付ける。
N社にもそのままの中国側の解釈では技術が中国側に第三者への移転を含め自由な使用を
認めることになるのも不満ではあった。
そこで私は白紙委任状を貰って2年近く続けたこのプロジェクト解散の役目を担うことになった。
当時このような経験をした日本企業は少なくなかったのである。
配送センター運営
無謀なコンペ出場から
業界最大手のS種苗会社が福岡県甘木市の配送センター運営をコンペで募集することになり、これに応募する。
競合する相手はいずれも日本で有数の物流会社ばかり。 各社は自社のシステムを利用した先進的な運営でアピールする。
これに対抗する私のプレゼンは「何も変えない」。 唯一の長所は他社に比べて「固定費用で安上り」。
これで受注に成功。これから改革に取り組みます。
現在では当たり前になったハンディ端末を使ったピッキング作業や棚卸、入庫・出荷の検品に加え、「苗」に特化したシステムを開発する。
苗には花の苗、野菜の苗などがあり、年間の販売計画に合わせ、多数の生産者が手分けして計画生産を行っています。
しかし、天候や病害など様々な原因で週単位に決められた納期にきちんと納品するのは易しいことではありません。
また、苗は見た目での識別が難しく、配送センターで出荷ミスが多数発生していました。
更に種物や苗は需要の季節要因が大きくセンター作業者の最適な確保ができずに悩みの種でした。
まず、生産者とのコミュニケーションが必要でした。
一見関係なさそうな配送センターと生産農家が連携して情報交換すると、
お互いの立場がわかり、協力しようという意識が働きます。
そこでこちらから鹿児島や宮崎県まで出向いて、苗の生育状況を見てまわり、生産者と話をします。
初めは農家の方も半信半疑でしたが、スムーズな物流が自分たちの利益にもつながることがわかり、
信頼関係が生まれました。
次に生産者との信頼関係をもとに、納入指示書を前もって生産者にメールまたはFAXします。
苗の生育や開花の具合などで納品に過不足が見込まれればこちらもその準備が可能です。
配送センター近隣の生産者には集荷時間の指定をする場合もあります。
入荷する苗は台車に乗せる苗トレーごとに品種を示すバーコードを貼り付け、入庫検品と出荷ミスを防止しました。
センター側は入庫に合わせて最適な出荷梱包ができるように柔軟な出荷指示を出せるような仕組みを作りました。
こうすることで、従来より10分の1の面積と、3分の1の時間で出荷ができるようになったのです。
これらの仕組みは私がこの配送センター事業から手を引いた後も使われ続けています。
目次へ